Delta T Demystified: How Thermal Differential Drives Data Center Efficiency
One of the most critical thermodynamic metrics in this domain is the Delta T (ΔT): the temperature differential between the supply and return air. Often misunderstood or underestimated, Delta T is a cornerstone in the efficiency, design and optimization of cooling infrastructure. In high-performance data centers, energy efficiency is not just a matter of sustainability—it directly affects operational expenditure and system reliability.
This article explores Delta T from an engineering and operational perspective, examining its influence on airflow dynamics, energy consumption, equipment reliability, and thermal efficiency. We’ll also explore how advanced monitoring solutions can be leveraged to manage and optimize Delta T in modern data centers.
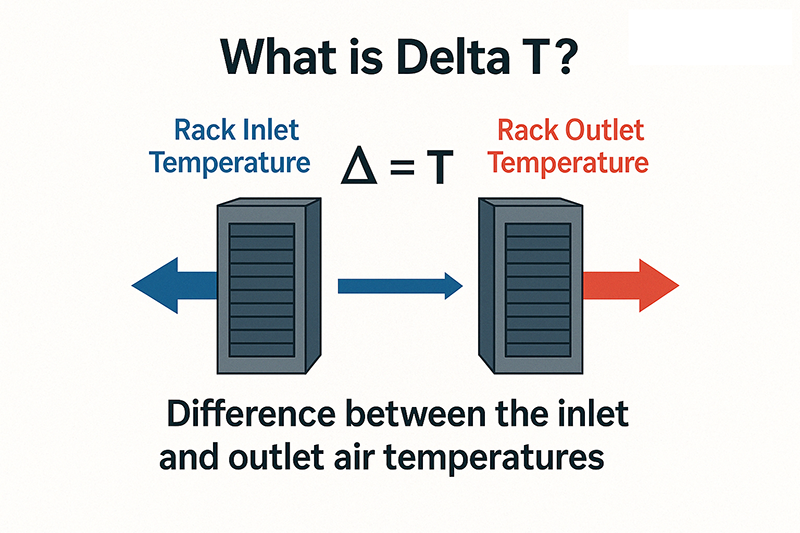
Understanding Delta T: More Than Just a Number
Delta T is commonly defined as:
ΔT = T_return – T_supply
This value represents the thermal energy removed from IT equipment, with T_supply typically measured at the front intake of server racks and T_return at the rear exhaust or CRAC/CRAH return vents.
However, measuring Delta T is not a one-size-fits-all calculation. Consider the following contexts:
CRAC/CRAH-level Delta T gives a macro-level overview of room cooling efficiency.
Rack-level Delta T captures micro-level inefficiencies, revealing recirculation or bypass conditions.
According to ASHRAE TC 9.9, maintaining an intake temperature between 18°C to 27°C (64.4°F to 80.6°F) is acceptable for most IT equipment. But the Delta T value itself can vary depending on airflow strategies, server densities, and cooling methods.
An optimal Delta T is typically within the 10°F to 20°F (5.5°C to 11°C) range. Values significantly lower or higher suggest cooling anomalies:
Too Low (e.g., 3–5°C): Cold air bypass—excess cooling not utilized.
Too High (e.g., 12–15°C+): Recirculation—hot exhaust air is mixing with intake.
The Thermodynamic Cost of Mismanaged Delta T
Delta T is intrinsically linked to the thermal transfer efficiency of your data center. A poorly optimized Delta T affects both cooling capacity and PUE (Power Usage Effectiveness).
Consider this real-world scenario:
Site A has a measured supply air temperature of 20°C and return air at 24°C (ΔT = 4°C). The low Delta T triggers CRAC units to increase airflow, consuming more fan energy without effectively cooling additional heat load.
Site B, with hot aisle containment and controlled airflow, achieves a return temperature of 30°C (ΔT = 10°C). Here, each unit of cold air absorbs more heat before returning, enabling higher CRAC efficiency and reduced energy consumption.
Mismanagement of Delta T leads to:
Increased chiller energy consumption due to higher load conditions
Over-delivery of conditioned air, creating stratification and pressure imbalance
Premature wear on cooling infrastructure due to overcompensation
Inefficient server thermal environments, increasing risk of hotspots
The 4 Delta T’s of a Data Center:
- IT Equipment Delta T : The temperature rise of air passing through IT equipment should be around 10°C to 20°C depending on equipment type. Blade servers with higher Delta T consume less airflow (CFM/kW) than “Pizza Box” servers with lower Delta T.
- Cooling Unit Delta T : Efficiency demands that the cooling unit’s air temperature matches the Delta T across IT equipment. Volumetric airflow (CFM) should also align with IT equipment flow rate.
- Supply Air Delta T : The temperature difference between the air leaving the cooling unit and arriving at the rack/server inlet. For maximum efficiency this should be 0°C, meaning non of the cooling energy is lost between the cooling unit and servers.
- Return Air Delta T : Return air temperature usually drops as it reaches cooling units. This contrasts with the practice of returning the warmest air, therefore for maximum efficiency the delta T between the server exhaust and the cooling air intake would be close to 0°C.
There is a simple calculation that can illustrate the difference ∆T can have with different IT equipment.
CFM = (3.16 x Watts) / ΔT
Where :
CFM = cubic feet per minute of airflow through the server
3.16 = factor for density of air at sea level in relation to ⁰F
ΔT = temperature rise of air passing through the server in ⁰F
A Blade server typically runs at higher ∆T. If we consider it consumes 400 Watts of power:
CFM = (3.16 x 400) / 35°F = 36 CFM
A typical pizza box style server runs at a lower ∆T but consumes the same power
CFM = (3.16 x 400) / 20°F = 63 CFM
So although both of these pieces of equipment consume the same power, their CFM cooling requirement is very different. That is why the ∆T is such an important metric. You need to balance the air supply from the cooling system with the demands of the servers. Too much and you waste energy overcooling, too little and servers can overheat.
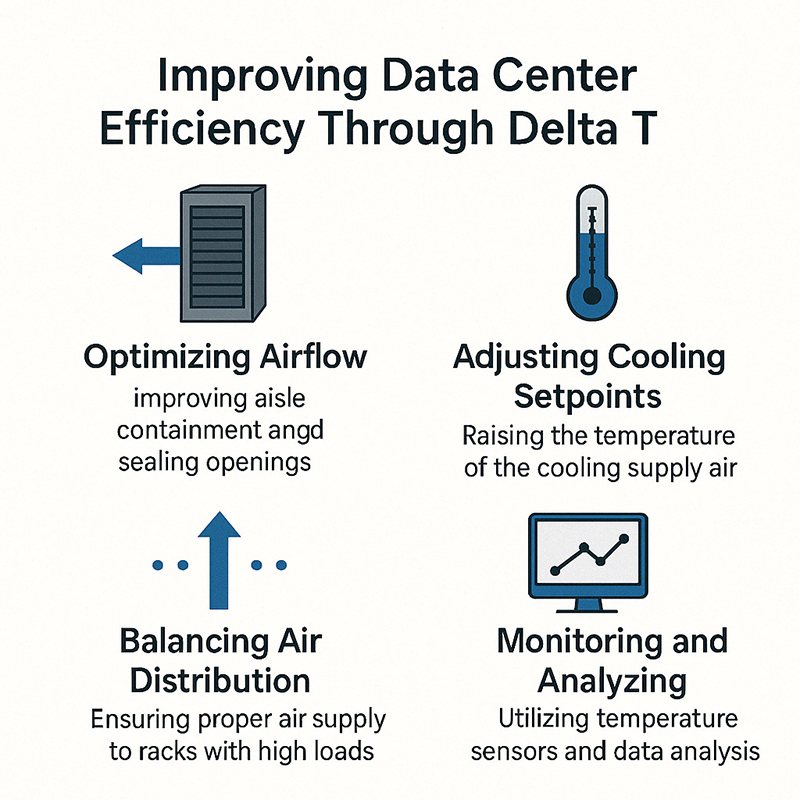
Diagnosing the Problem: Measuring and Mapping Delta T
Delta T should be measured at both system and rack levels to properly diagnose inefficiencies.
Key Measurement Techniques:
Thermal Map Sensors: AKCP’s Cabinet Thermal Map sensors provide three-point data—top, middle, and bottom of rack—both at intake and exhaust. This detailed mapping enables operators to see vertical heat stratification and uneven airflow distribution.
CRAC Unit Telemetry: Return/supply air temperatures logged at the CRAC level provide a cumulative Delta T across the white space.
Differential Pressure Sensors: Paired with temperature sensors, they can identify plenum air velocity issues or blockages.
Advanced DCIM platforms overlay this data in real time, allowing for visual interpretation of thermal imbalances and environmental anomalies.
Managing Delta T: Engineering-Level Approaches
Containment Architectures
Containment remains one of the most impactful strategies for Delta T optimization.
Cold Aisle Containment (CAC) isolates cold air to the server intake path, minimizing bypass.
Hot Aisle Containment (HAC) captures and directs hot exhaust air back to CRAC units without recirculating into the data hall.
Impact: Studies by Uptime Institute and ASHRAE report Delta T improvements of 4–7°C, with energy savings upwards of 25% in some deployments.
Airflow Control and Balancing
Proper airflow distribution ensures that the cooling load matches the IT thermal output. This includes:
Variable Air Volume (VAV) control in CRACs
EC fans in server racks and containment corridors
Balancing perforated floor tile placement to only deliver air where needed
Using computational fluid dynamics (CFD) in conjunction with sensor data helps validate airflow assumptions made during initial design.
Rack Hygiene and Path Integrity
An often-neglected area, physical management within racks plays a huge role:
Use blanking panels to prevent front-to-rear short-circuiting
Seal all cable passthroughs
Avoid rear cable congestion that may disrupt airflow
An unobstructed airflow path is critical to achieving full Delta T potential.
Delta T in Practice: A Data Center Efficiency Case Study
Facility Type: Tier III colocation
Location: Singapore
Initial Conditions:
CRAC Supply Temp: 19.5°C
Return Temp: 23.1°C
Delta T: 3.6°C
Cooling Energy Use: 34% of total facility load
Intervention:
Installed AKCP thermal map sensors on all racks
Deployed hot aisle containment
Optimized perforated tile layout
Sealed cable penetrations
Post-Optimization:
CRAC Supply Temp: 20.5°C
Return Temp: 30.2°C
Delta T: 9.7°C
Cooling Energy Use: 22% of total load
ROI on upgrades: 13 months
Toward Net-Zero: Delta T’s Role in Sustainable Data Centers
As the industry accelerates toward carbon neutrality and increasingly stringent energy efficiency mandates, Delta T management provides a clear path to:
Lowering facility PUE
Enhancing equipment longevity
Reducing reliance on mechanical cooling
When paired with liquid cooling, free cooling, or waste heat reuse strategies, high Delta T values can contribute to advanced energy reuse schemes, such as district heating or process heat recovery.
Final Thoughts
Delta T is not a passive measurement; it’s a diagnostic and control mechanism. By transforming Delta T from a static number to a live feedback tool, operators can tune their thermal environments with surgical precision.
With sensor-driven intelligence and a holistic airflow strategy, Delta T management becomes a lever not just for operational excellence but also for long-term sustainability.
One Response