Corrosion: How To Prevent The Threat In Data Center?
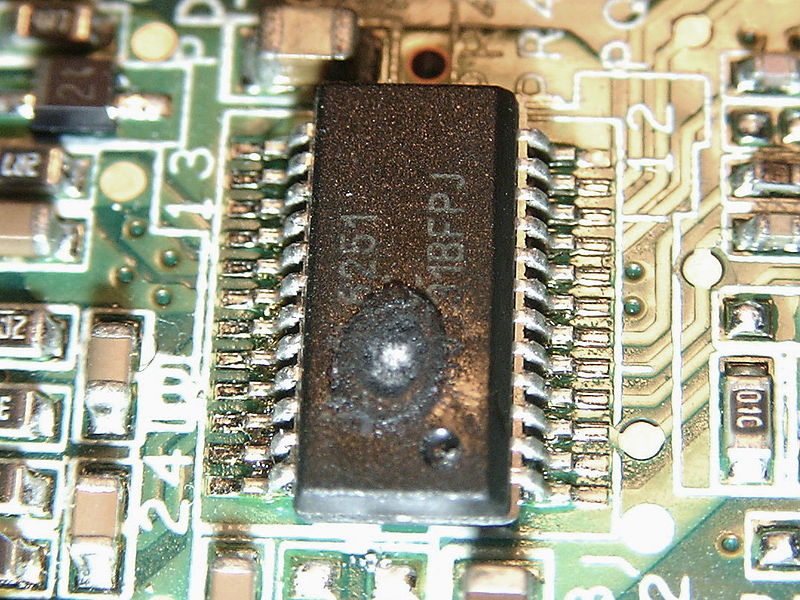
Causes And Consequences Of Corrosion
Corrosion can occur in data center-free cooling system components such as air to water heat exchangers, resulting in major efficiency and availability difficulties.
Destructive Effects
Types Of Corrosion
Close Contact
Liquid Asset
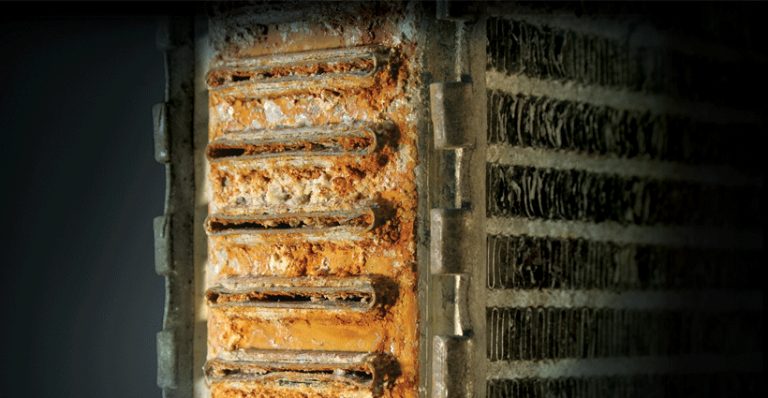
Hard Talk
How To Prevent Corrosion?
Data Center Design and Operation Requirements
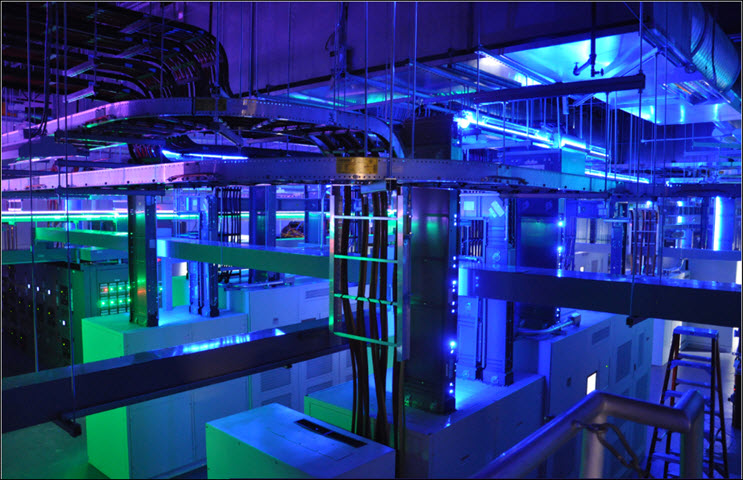
Maintenance, infrastructure, and equipment upgrades occur on a regular basis. However, if not handled with care, these seemingly routine actions could result in the introduction of airborne pollutants.
Even data centers in places where air quality is not an issue may struggle to maintain a safe environment for sensitive electronic equipment due to the rising use of air-side economizers for free cooling. Any air utilized for these purposes should be purified before being introduced into the data center.
To eliminate airborne contaminants and meet warranty requirements for new IT and datacom equipment. Datacenter owners and operators must take the following action:
- Measure the corrosion rates both within and outside the data center.
- Seal all doors, windows, and wall penetrations in the data center.
- If the data center envelope is built to be positively pressurized, install room pressure monitors.
- Measure airflow at the supply and exhaust air grills, and at each computer room air-conditioning (CRAC) unit.
- Develop a temperature and humidity profile.
Datacenter managers must monitor and mitigate both gaseous and particle contamination in their facilities in order to ensure hardware reliability. ASHRAE has established standards that outline allowable contamination levels in collaboration with many of the world’s leading computer system vendors.
Environmental Assessments
ISA Standard 71.04-2013, presents a simple quantitative approach for determining airborne corrosivity in a data center environment. The “reactivity monitoring” method entails using copper and silver sensors that have been exposed to the environment for a length of time in order to evaluate corrosion layer thickness and chemistry. The evaluation includes silver reactivity monitoring, which provides a detailed accounting of the types of corrosive chemical species present in the data center.
For electrical and electronic systems, ISA 71.04 identifies four levels of environmental severity, providing a gauge of the environment’s corrosion potential. The higher the total copper and silver reactivity rates, the higher the overall categorization.
Corrosion Monitoring
When it comes to air quality monitoring for data center applications, there are numerous solutions to consider. Monitoring of outdoor and ambient air at various locations inside and outside the data center is required for the proper assessment of environmental conditions in the data center. Furthermore, room size and layout should be considered when determining the right placement and kind of CCCs, which can aid in determining compliance with air-quality criteria, as well as real-time atmospheric corrosion monitors (ACM). Data from the ACMs can aid in the statistically reliable assessment of corrosion rates and corrosion control measures in the environment. Either monitoring method can offer the information needed to troubleshoot and minimize contamination issues within the data center.
CCCs are often used for an initial survey of ambient air quality and the data center environment, and they can also be utilized to give historical data on an ongoing basis. This is especially significant when equipment warranties stipulate that an ISA Class G1 environment be established and maintained. Seasonality is a significant issue, and outdoor air should be evaluated at various periods throughout the year.
Real-time monitoring is also possible but should be restricted to the data center. ACMs placed in a number of areas can help establish if contamination is widespread or limited to a specific area when corrosion concerns have been discovered. After establishing a baseline, some of the monitors could be repositioned around the issue area to assess the efficacy of pollution control techniques. Once the data center environment is under control and meets the manufacturer’s warranty requirements, the optimum permanent ACM locations for specific applications can be determined.
Corrosion monitoring can be utilized to identify pollutant types such as active sulfur, sulfur oxides, and inorganic chloride with high confidence. These conclusions can be confirmed using independent sources of environmental data to confirm the corrosion monitoring results.
AKCP Wireless Air Quality Sensor
AKCP Air Quality Monitoring System detects levels of hazardous gases such as SO2, H2S, and CO in the data center. These gases are known to be hazardous to the data center equipment.
- Acetone (eg. paints and glues)
- Toluene (eg. furniture)
- Ethanol (eg. perfume, cleaning fluids)
- Hydrogen Sulfide (eg. decaying food)
- Benzene (eg. Cigarette smoke)
AKCP Wireless Temperature And Humidity
This wireless sensor maintains required ambient conditions, log and graph data over time, and receive real-time alerts when user-defined sensor criteria are exceeded. When in range, use as a data logger with data buffered and synchronized to the gateway.
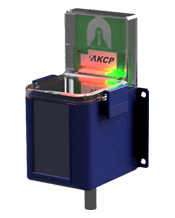
- 4x AA Battery powered, with 10-year life*
- 4x AA Batteries with 10 years guaranteed battery life*
- 5VDC or 12VDC powered
- IP66 rated waterproof enclosure
- LED indicators for power, status, and RSSI
- Optional DIN rail or pipe mounting accessories
- Optional cable up to 15ft for sensor placement
Conclusion
Reference Links:
https://theshopmag.com/wp-content/uploads/2019/07/corrosion-radiator
https://latem.com/blog/prevent-corrosion-metal-parts.htm
https://www.sciencedirect.com/science/article/pii/B9780857096807500012
How to Prevent Rust: 9 Ways for Any Situation